Advanced Nuclear Energy Is Coming to U.S. Military Bases
A reliable energy supply is key to a prepared and effective military, especially considering the amount of digital and electric domestic infrastructure used today. Approximately 95% of the U.S. Department of Defense’s (DoD) military bases are powered by the existing regional grid, making it the foundation for national defense. The Trump administration’s four nuclear energy executive orders recognize the role advanced nuclear technology can play in securing reliable power for both military and civilian use, marking a bold vision for an energy-dominant America that leads the world in nuclear energy deployment. These orders prioritize rapid reactor deployment, set a goal of quadrupling nuclear capacity to 400 GW by 2050, direct the DoD to demonstrate military applications of advanced nuclear energy and outline a whole-of-government approach to streamline licensing and revitalize domestic nuclear energy and fuel infrastructure.
In addition to providing a dedicated power supply to support these efforts, a reliable grid with a robust transmission system is key to ensuring certainty for national security. Avoiding power disruptions is essential to maintaining mission readiness, communications and defense operations. By securing their own reliable energy supply, military bases reduce vulnerability to grid failures, cyberattacks and fuel supply chain disruptions, ensuring consistent operational capability in both peacetime and conflict.
May 2025 Executive Order: Deploying Advanced Nuclear Reactor Technologies for National Security
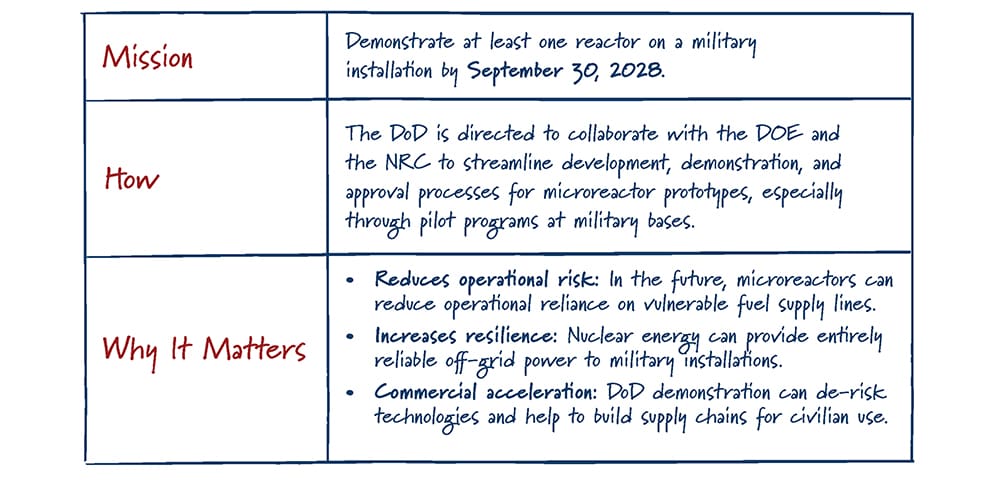
Sources: Whitehouse.gov
The Deploying Advanced Nuclear Reactor Technologies for National Security executive order tasks the DoD with demonstrating at least one advanced nuclear reactor on a military installation by September 30, 2028, a clear milestone that aligns with previous initiatives in the DoD and Defense Innovation Unit (DIU). To achieve this, they will collaborate closely with the Department of Energy (DOE) and the Nuclear Regulatory Commission (NRC) to streamline development, testing and approval processes, focusing on pilot microreactor programs at military bases. This effort can reduce the military’s dependence on vulnerable fuel supply lines and enhance the energy resilience of installations through reliable off-grid power. Additionally, these efforts can have transformative effects on the broader nuclear energy industry. Establishing a steady pipeline of military-led advanced reactor projects can help build out an order book that enables more predictable demand for manufacturers, encourages investment in domestic supply chains and promotes regulatory certainty that can significantly lower costs over time. As more units are built and deployed, economies of scale and standardization can help bend the cost curve, making advanced nuclear reactors more accessible for commercial use.
This push to leverage nuclear innovations to support defense capabilities mirrors history. Naval reactors, first developed in 1954, pioneered many design innovations and critical safety protocols that paved the way for the first civilian power plants. The DoD could jump-start the civilian nuclear industry again by procuring and de-risking advanced reactor technology.
Existing DoD Advanced Nuclear Energy Initiatives
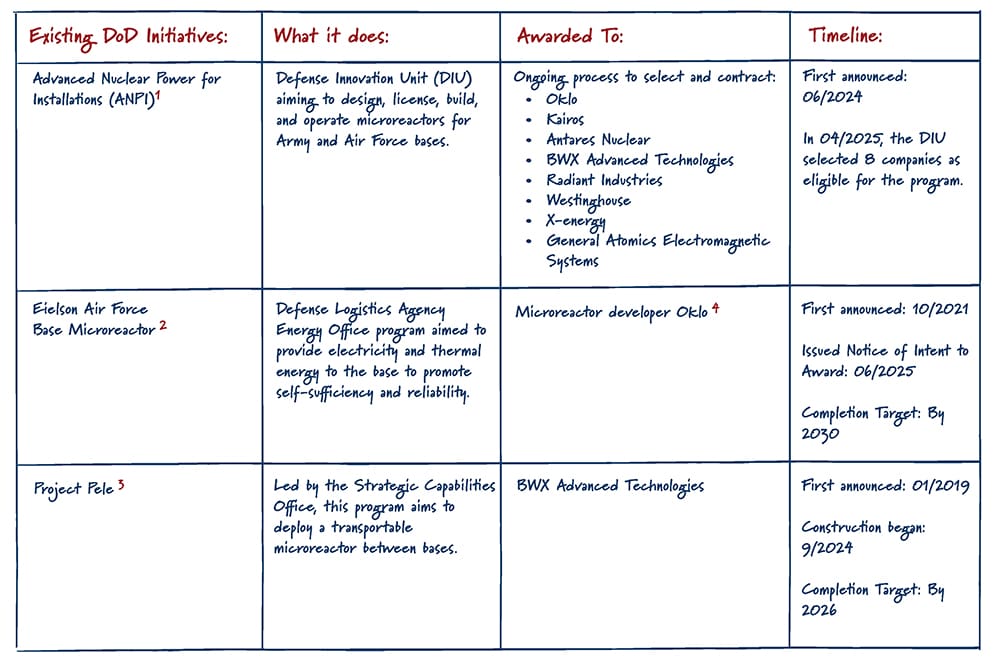
Sources: 1. Advanced Nuclear Power for Installations (ANPI), 2. Air and Space Forces Magazine, 3. ClearPath, 4. American Nuclear Society
Overall, President Trump’s nuclear energy executive orders represent a strategic connection between national defense and energy independence. By placing advanced nuclear technologies at the core of military reliability and broader energy security, these initiatives create a forward-looking framework for public-private collaboration. The potential results following recent DoD initiatives and executive orders not only enhance military readiness but also revitalize the U.S. nuclear industry by providing an early demand signal. Ultimately, this effort lays the foundation for a clean, secure and self-reliant energy future for the military.