Clean Energy Innovation Academy Brings Congressional Staff to Cleveland, Ohio
Steel is the backbone of America’s economy, and is a necessary material for critical infrastructure like roads, bridges, buildings, and appliances. It is a useful, and impactful metal; however, its production accounts for eight percent of total global emissions. But here in the U.S., we actually produce the cleanest steel of the top seven steel-producing countries.
So that’s why Cleveland, Ohio was a perfect stop for ClearPath’s Clean Energy Innovation Academy (CEIA). CEIA, launched in 2020, is an ongoing educational series for Congressional staff focused on conservative clean energy and industrial technology and policy.
We were excited to bring a delegation of seven Congressional staff members to Cleveland this year. The delegation consisted of professional staff who work for Members of Congress on the House Ways and Means, House Appropriations, and House Science, Space, and Technology Committees, as well as Committee Professional Staff Members from the House Energy and Commerce, and House Science, Space, and Technology Committees.
These staff joined us to expand their understanding of how U.S. companies are reducing emissions in the industrial sector, and the opportunities to further ensure that the United States leads the world in affordable, low-emissions materials, like steel, cement, and concrete.
“This trip offered a new perspective on how America produces the cleanest steel in the world and the exciting opportunities to further decarbonize the industrial sector. We’re excited to get to work on the Hill to advance policies that encourage domestic production of steel, where Americans will benefit from more jobs, cleaner products, and lower prices.”
– Emily Henn, Legislative Director for Rep. Carol Miller (R-WV)
Cleveland-Cliffs’ Cleveland Works Steel Facility
Cleveland is home to the Cleveland-Cliffs Cleveland Works steel facility, a site known for its low-emissions steelmaking processes and U.S.-based manufacturing capabilities. According to the company, Cleveland Works is recognized as one of the most productive integrated facilities in the world for completing the entire process of steelmaking, from smelting iron ore to the finished rolled product. This facility supplies steel that is used in everyday products, such as the roll cages in vehicles. Directly employing more than 2,000 workers and hundreds of contractors, this facility is an economic anchor for the city.
Cleveland-Cliffs is also well-known for its dedication to low-emissions practices, producing steel well below the global carbon intensity of blast furnace-basic oxygen furnace (BF-BOF) steel. Their emissions reduction success relies on readily-available technologies such as using hot briquetted iron (HBI) in existing blast furnaces, which reduces emissions from producing new iron, and replacing pulverized coal with natural gas in their furnaces.
Cleveland Cliffs is committed to forward-looking investments that reduce their emissions and maintain global competitiveness. Take the newly operational plant in Toledo, Ohio for example. It uses natural gas to produce hot briquetted iron (HBI) through the direct reduced iron (DRI) process, which lowers steel emissions by 50% without compromising product reliability. This facility can adopt up to 70% clean hydrogen with marginal retooling to further reduce emissions and avoid resourcing from countries like China. Another example includes a carbon capture and sequestration (CCS) project at their facility in Burns Harbor, Indiana, which aims to capture and sequester 2.8 million tons of CO2 per year, a massive emissions reduction effort.
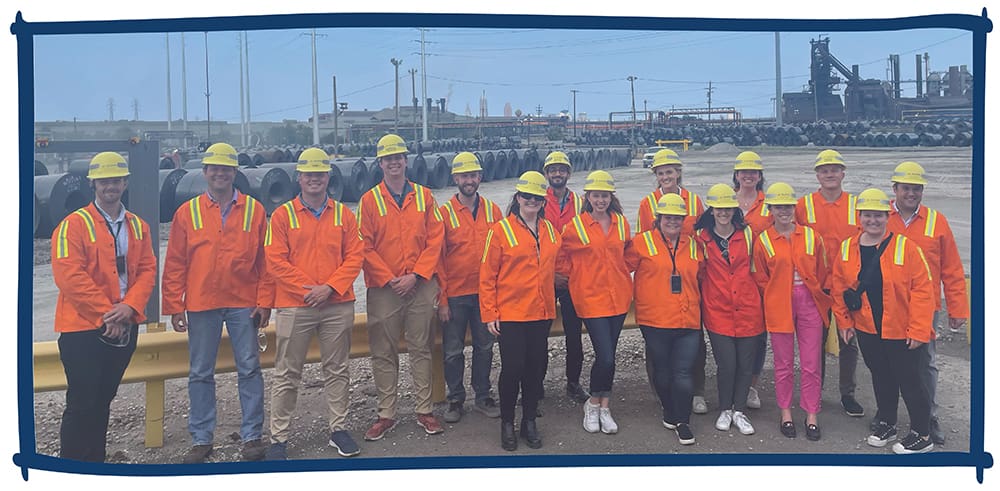
Front Row L to R: Emily Johnson, Sarah Alexander, Dana Faught, Mallory Shaevsky, Ivy English, Amanda Sollazzo
Back Row: Ray Phillips, Luke Bolar, Steve Hansen, Chase Hite, Niko McMurray, Rafae Ghani, Dillyn Carpenter, Emily Henn, Danny Hartl, Jeremy Harrell
By seeing literal “steel in the ground” projects at Cleveland-Cliffs’ Cleveland Works steel facility, Congressional staff learned about industrial decarbonization efforts underway through a tour of the steelmaking process including how molten steel is shaped into finished products and treated with chemicals for better strength, helping them to better understand steel production processes and new innovations to produce it cleaner.
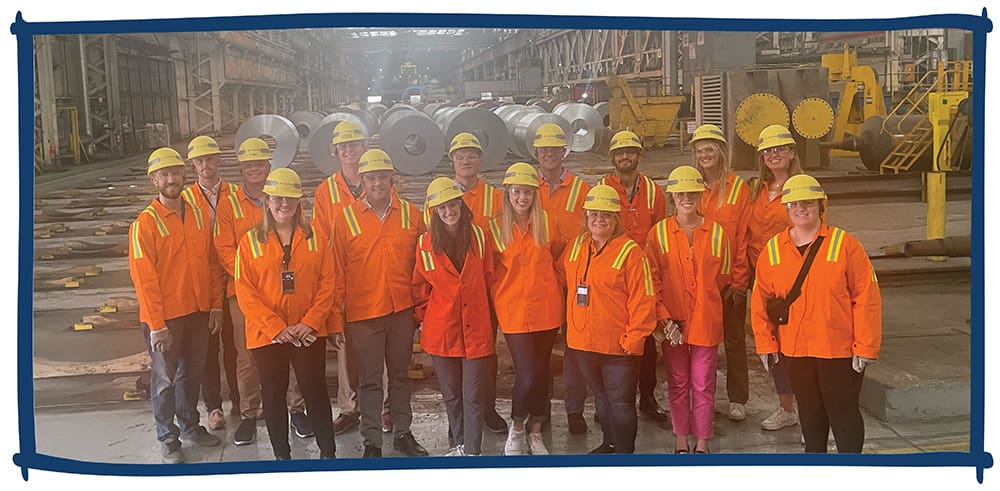
Following the tour, the staff attended dinner with Dr. Mark Peters, the Executive Vice President for National Laboratory Management and Operations at Battelle, who previously served as the Lab Director at Idaho National Lab. The dinner discussion focused on how National Labs play a vital role in research, development, and deployment efforts and how public-private partnerships can be utilized to spur innovation.
The delegation returned to D.C. with a concrete understanding of how companies are starting to successfully produce low-emissions industrial materials and the areas of opportunity to ensure the U.S. is a global leader in industrial manufacturing, all while reducing global emissions. ClearPath looks forward to continuing its Clean Energy Innovation Academy in 2024!